Création d'un boîtier sur mesure pour l'électronique
Introduction
Lors de la réalisation d'un premier montage électronique ou d'un prototype fonctionnel, la conception d'un boîtier n'est souvent pas une priorité. Pourtant, c'est souvent ce qui limite la finalisation d'un circuit imprimé abouti.
À l'inverse, concevoir un boîtier trop tôt peut imposer des contraintes qui freinent le développement et la créativité du projet. Il n'y a pas de mauvaise approche, mais il existe des méthodes pour faire avancer chaque aspect jusqu'à ce qu'ils s'intègrent parfaitement.
C'est précisément le cas d'une demande récente du Fablab19 pour un boîtier pour contenir un serveur de messagerie par SMS. Les contraintes étaient claires :
- Déporter une antenne à l'extérieur du boîtier pour éviter toute interférence avec une antenne interne.
- Protéger les circuits tout en permettant une installation externe sur un boîtier serveur.
- Assurer l'évacuation de la chaleur générée par les circuits internes, tout en conservant un design simple et fonctionnel.
- Intégrer tous les composants électroniques et prévoir une trappe d'accès à une prise USB en cas de panne.
- Ajouter un marquage pour identifier facilement le boîtier.
Nous utilisons régulièrement des outils open-source et nous sommes ouverts à l'open hardware. Notre objectif est de concevoir et de partager nos solutions avec les membres du Fablab19, afin que le projet soit évolutif et résilient.
Étape 1 : Modélisation des circuits
La première étape consiste à modéliser les circuits électroniques. L'objectif est de positionner chaque carte dans l'espace, puis de concevoir la base du boîtier, qui servira de support.
Nous aurions pu optimiser l'espace interne pour minimiser la taille du boîtier. Mais que se passe-t-il si, plus tard, nous devons ajouter des câbles ou une batterie de secours ? En anticipant cette évolution, nous avons volontairement laissé de la place là où c'était possible.
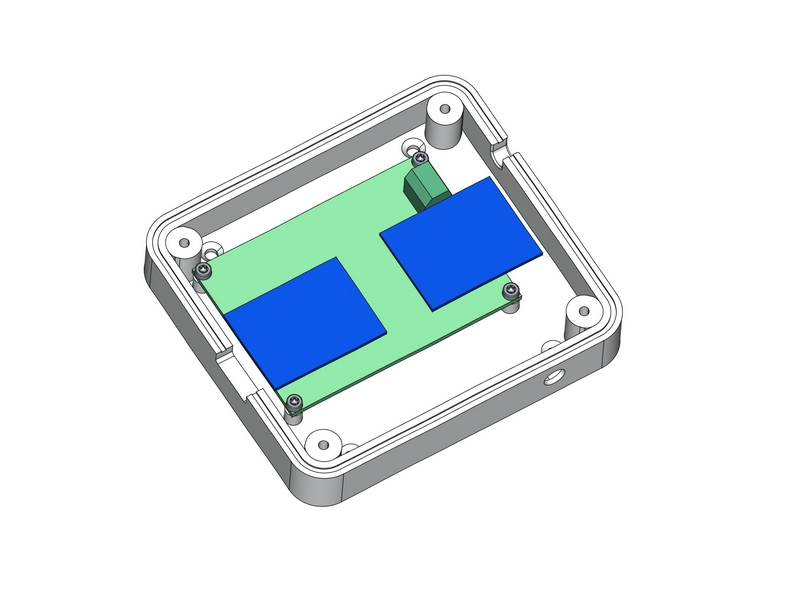
Étape 2 : Finalisation du design interne
Une fois la base du boîtier conçue, nous avons défini les emplacements des vis et vérifié que l'assemblage se ferait sans difficulté. Une fois cette validation effectuée, nous avons imaginé un système d'aération pour faciliter la dissipation de la chaleur.
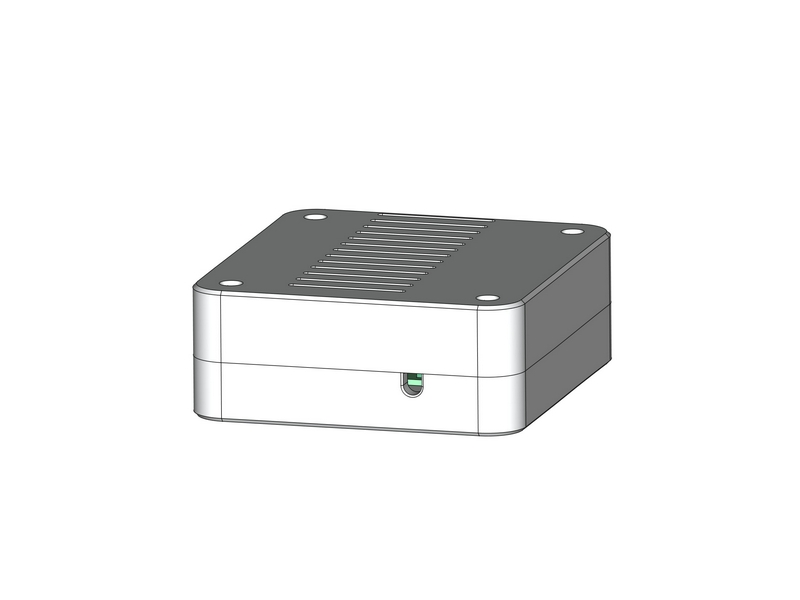
Étape 3 : Test d'assemblage
Nous avons ensuite testé l'assemblage des deux parties du boîtier en ajoutant les jeux nécessaires pour un montage fluide et sans contrainte mécanique.
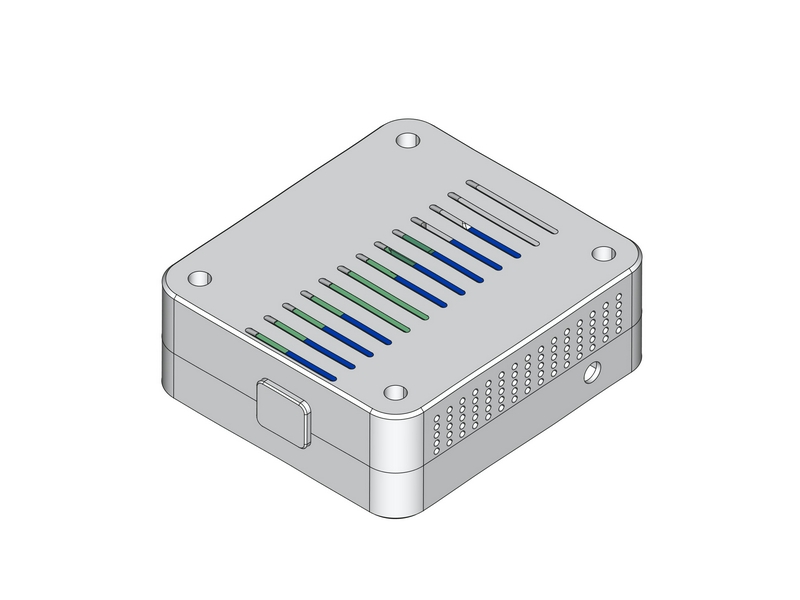
Étape 4 : Personnalisation du boîtier
La dernière étape a consisté à intégrer des éléments graphiques au boîtier pour le personnaliser. Pour cet exemple, nous avons utilisé des fichiers SVG et une machine d'impression récente permettant d'inscrire le nom et la fonction du boîtier directement sur sa surface.
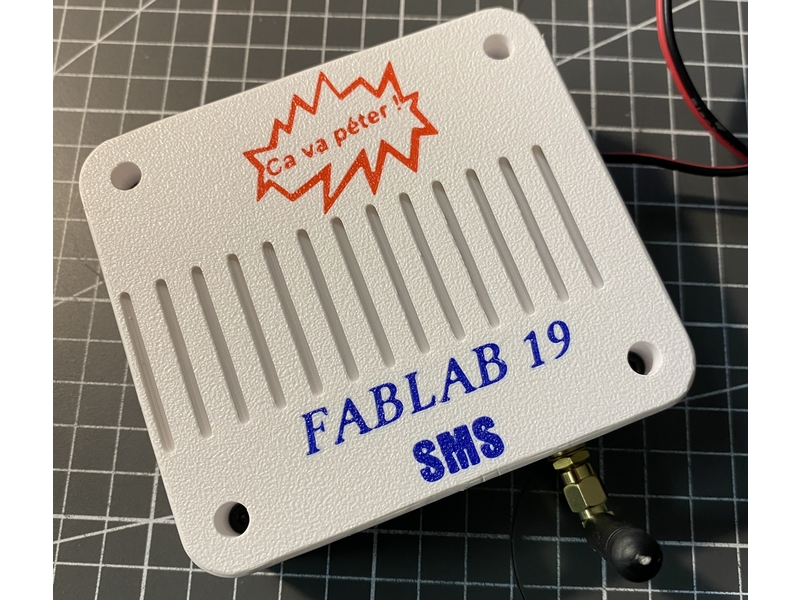
Conclusion
Grâce à une approche rigoureuse, nous avons respecté le cahier des charges tout en intégrant une personnalisation sur mesure. Avec l'autorisation du Fablab19, nous avons pu tester et graver les marquages directement sur le boîtier. Ce projet nous a permis de confirmer que nous pouvons concevoir et fabriquer des boîtiers sur mesure pour des électroniques basse tension, adaptées aux besoins de l'IoT.